Encoder Def Block: Difference between revisions
No edit summary |
No edit summary |
||
Line 15: | Line 15: | ||
! scope="col" style="width: 50%;"|Description | ! scope="col" style="width: 50%;"|Description | ||
|- | |- | ||
!Pattern | !Crank Pattern | ||
| | | | ||
|The pattern in which the Crank/CAM will be encoded | |||
|- | |- | ||
! | ! Firing Order | ||
| | | Array | ||
| | |The order in which the cylinders will be encoded. Values must inputted in an array format within brackets. Ensure your device is wired correctly (See below for example) | ||
|- | |- | ||
! | !Cycle Type | ||
| | | | ||
|The type of cycle used in encoding | |||
|- | |- | ||
! | !Camshafts | ||
| | | | ||
|The number of CAM shafts used | |||
|} | |} | ||
==Calibration Setup Example== | |||
<p>As an example, the configuration as in the picture above would have the following configuration and calibrations: | |||
- Crank/cam pattern: 60 Minus 2, 4-Lobe Cam | |||
- Firing order: 1-8-7-2-6-5-4-3 | |||
- Cycle Type: 4-stroke | |||
- Number of Cams: 1 | |||
- Epm_numCyl_C (count): 8 | |||
- FiringOrder: [1 8 7 2 6 5 4 3] | |||
- Epm_phiTdc1_C (CAD): 72 | |||
- EpmCaS_phiSegOfs_CA (CAD): 48 | |||
- EpmCaS_phiSegLen_CA (CAD): [156 144 36 24 0 0 0 0 0 0] | |||
- EpmCaS_dSegSeries_CA (bitfield): [67 16 97 18 65 18 67 48] | |||
o Bit 0-3: [3 0 1 2 1 2 3 0] | |||
o Bit 4: [0 1 0 1 0 1 0 1] | |||
o Bit 5: [0 0 1 0 0 0 0 1] | |||
o Bit 6: [1 0 1 0 1 0 1 0] | |||
- EpmCaS_numSegSerLst_C (count): 7 | |||
- EpmSeq_phiInt_CA (degBTDC): [78 0] | |||
- EpmSeq_phiStrtInt_CA (degBTDC): [78 0] | |||
Other important calibrations to be set correctly (per Bosch): | |||
- Epm_phiGap2Zero_C (CAD): 0 | |||
- EpmSeq_nMaxStrtInt_C (rpm): 550 | |||
- EpmRRS_nEngMax_C (rpm): 0 | |||
- EpmSeq_swtInt_C (bitfield): 1 | |||
- Epm_nNoSyncVerify_C: 100 | |||
</p> | |||
==Injector and Coil Wiring on the ECM196:== | |||
<p> | |||
Interfaces to Raptor engine blocks (such as the spark and injector block) are in physical cylinder order; underneath the hood, Raptor references the FiringOrder calibration to assign the commands to the correct resource. | |||
On the ECM196, the injector and coil outputs always actuate sequentially 1, 2, 3, 4, etc., and thus firing order must also be enforced through proper wiring. As an example, if the firing order is 1-8-7-2-6-5-4-3, the injectors and coils must be wired according to the following: | |||
Fire Order Number | |||
TDC (degATDC1) | |||
Physical Cylinder Number | |||
Injector Resource and Pin | |||
Coil Resource and Pin | |||
1 | |||
0 | |||
1 | |||
OUTPUT13 (K022) | |||
OUTPUT56 (A051) | |||
2 | |||
90 | |||
8 | |||
OUTPUT14 (K090) | |||
OUTPUT57 (A072) | |||
3 | |||
180 | |||
7 | |||
OUTPUT15 (K023) | |||
OUTPUT58 (A052) | |||
4 | |||
270 | |||
2 | |||
OUTPUT16 (K074) | |||
OUTPUT59 (A073) | |||
5 | |||
360 | |||
6 | |||
OUTPUT17 (K040) | |||
OUTPUT60 (A049) | |||
6 | |||
450 | |||
5 | |||
OUTPUT18 (K091) | |||
OUTPUT61 (A070) | |||
7 | |||
540 | |||
4 | |||
OUTPUT19 (K030) | |||
OUTPUT62 (A050) | |||
8 | |||
630 | |||
3 | |||
OUTPUT20 (K032) | |||
OUTPUT66 (A071) | |||
</p> | |||
==Other ECM196 encoder items to note:== | |||
<p>- Even if the shutdown task is called (through the Raptor Shutdown block), the ECM196 module will not turn off if there is a non-zero engine speed reading; it will remain in a "post-drive wait" state, in which the background tasks and CAN communications are active. | |||
- The encoder performs in cam backup mode (ie, wasted spark with ignition events happening on both phases) (status = CamBackup) only if a start transition (0 speed to a non-zero speed) occurs without the cam signal present. If instead the cam signal is lost after engine speed has already been seen and crank/cam have fully synchronized, the encoder continues to perform as normal (status = OK) and fully synchronized (SynState = FullSync) as the ECM does not need the cam signal to determine phase at that point (as it remembers it when determined previously when the cam signal was present). | |||
- To exit cam backup mode (status = CamBackup) and perform as normal (status = OK), one of the following scenarios must occur: | |||
o The ECM must see the cam signal on a halt transition (ie, from non-zero speed to 0 speed). | |||
o The ECM goes through a power cycle. | |||
In these cases, the encoder will perform as normal (status = OK) on the next start transition (0 speed to a non-zero speed) as long as the cam signal is present at that time.</p> |
Latest revision as of 17:46, 14 September 2023
Return to the main Raptor page
Return to Raptor-Dev Engine Library
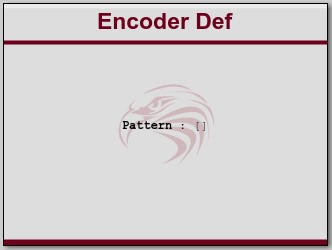
Description
This block defines the crank shaft encoder. This block must be in the top-level of the model in order to use and angle-based blocks.
Parameters
Parameter | Type | Description |
---|---|---|
Crank Pattern | The pattern in which the Crank/CAM will be encoded | |
Firing Order | Array | The order in which the cylinders will be encoded. Values must inputted in an array format within brackets. Ensure your device is wired correctly (See below for example) |
Cycle Type | The type of cycle used in encoding | |
Camshafts | The number of CAM shafts used |
Calibration Setup Example
As an example, the configuration as in the picture above would have the following configuration and calibrations: - Crank/cam pattern: 60 Minus 2, 4-Lobe Cam - Firing order: 1-8-7-2-6-5-4-3 - Cycle Type: 4-stroke - Number of Cams: 1 - Epm_numCyl_C (count): 8 - FiringOrder: [1 8 7 2 6 5 4 3] - Epm_phiTdc1_C (CAD): 72 - EpmCaS_phiSegOfs_CA (CAD): 48 - EpmCaS_phiSegLen_CA (CAD): [156 144 36 24 0 0 0 0 0 0] - EpmCaS_dSegSeries_CA (bitfield): [67 16 97 18 65 18 67 48] o Bit 0-3: [3 0 1 2 1 2 3 0] o Bit 4: [0 1 0 1 0 1 0 1] o Bit 5: [0 0 1 0 0 0 0 1] o Bit 6: [1 0 1 0 1 0 1 0] - EpmCaS_numSegSerLst_C (count): 7 - EpmSeq_phiInt_CA (degBTDC): [78 0] - EpmSeq_phiStrtInt_CA (degBTDC): [78 0] Other important calibrations to be set correctly (per Bosch): - Epm_phiGap2Zero_C (CAD): 0 - EpmSeq_nMaxStrtInt_C (rpm): 550 - EpmRRS_nEngMax_C (rpm): 0 - EpmSeq_swtInt_C (bitfield): 1 - Epm_nNoSyncVerify_C: 100
Injector and Coil Wiring on the ECM196:
Interfaces to Raptor engine blocks (such as the spark and injector block) are in physical cylinder order; underneath the hood, Raptor references the FiringOrder calibration to assign the commands to the correct resource. On the ECM196, the injector and coil outputs always actuate sequentially 1, 2, 3, 4, etc., and thus firing order must also be enforced through proper wiring. As an example, if the firing order is 1-8-7-2-6-5-4-3, the injectors and coils must be wired according to the following: Fire Order Number TDC (degATDC1) Physical Cylinder Number Injector Resource and Pin Coil Resource and Pin 1 0 1 OUTPUT13 (K022) OUTPUT56 (A051) 2 90 8 OUTPUT14 (K090) OUTPUT57 (A072) 3 180 7 OUTPUT15 (K023) OUTPUT58 (A052) 4 270 2 OUTPUT16 (K074) OUTPUT59 (A073) 5 360 6 OUTPUT17 (K040) OUTPUT60 (A049) 6 450 5 OUTPUT18 (K091) OUTPUT61 (A070) 7 540 4 OUTPUT19 (K030) OUTPUT62 (A050) 8 630 3 OUTPUT20 (K032) OUTPUT66 (A071)
Other ECM196 encoder items to note:
- Even if the shutdown task is called (through the Raptor Shutdown block), the ECM196 module will not turn off if there is a non-zero engine speed reading; it will remain in a "post-drive wait" state, in which the background tasks and CAN communications are active. - The encoder performs in cam backup mode (ie, wasted spark with ignition events happening on both phases) (status = CamBackup) only if a start transition (0 speed to a non-zero speed) occurs without the cam signal present. If instead the cam signal is lost after engine speed has already been seen and crank/cam have fully synchronized, the encoder continues to perform as normal (status = OK) and fully synchronized (SynState = FullSync) as the ECM does not need the cam signal to determine phase at that point (as it remembers it when determined previously when the cam signal was present). - To exit cam backup mode (status = CamBackup) and perform as normal (status = OK), one of the following scenarios must occur: o The ECM must see the cam signal on a halt transition (ie, from non-zero speed to 0 speed). o The ECM goes through a power cycle. In these cases, the encoder will perform as normal (status = OK) on the next start transition (0 speed to a non-zero speed) as long as the cam signal is present at that time.