Natural Gas Engine with Variable Energy Adjustment: Difference between revisions
Line 18: | Line 18: | ||
[[File:Arrow_Cal_Manual.jpg|thumb |upright=1.5|alt=Calibration manual for a natural gas engine for stationary power generation.|Natural Gas Engine Control System Calibration Manual]] | [[File:Arrow_Cal_Manual.jpg|thumb |upright=1.5|alt=Calibration manual for a natural gas engine for stationary power generation.|Natural Gas Engine Control System Calibration Manual]] | ||
The '''[[MotoHawk-Platform|MotoHawk]]''' and New Eagle toolchains were employed to accelerate development. Using the | The '''[[MotoHawk-Platform|MotoHawk]]''' and New Eagle toolchains were employed to accelerate development. Using the MATLAB/Simulink environment, the team was able to unit test and integrate the model in the simulation environment. The algorithm was then quickly deployed to the ECM through the integrated build environment. | ||
Arrow used the '''[[MotoTune]]''' calibration tool to calibrate the engine parameters. New Eagle supplied Arrow with a calibration manual so that they could properly tune the engine for their application. | Arrow used the '''[[MotoTune]]''' calibration tool to calibrate the engine parameters. New Eagle supplied Arrow with a calibration manual so that they could properly tune the engine for their application. |
Revision as of 19:25, 24 February 2023
Opportunity
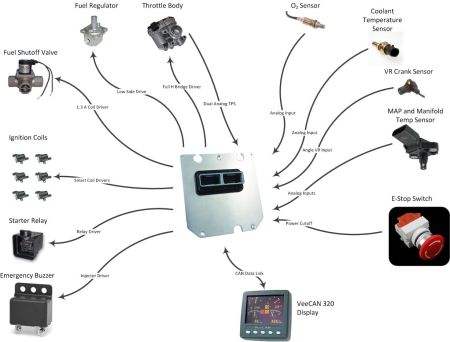
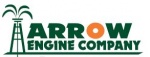
New Eagle developed the control system on a stationary natural gas engine for Arrow Engine Company. The engine provides power generation in oil and gas exploration sites and must run on the fuel obtained directly from the field. The energy content of the fuel and the level of contaminants varies from site to site. The end customer required adjustable controls to optimize the engine operation for the particular BTU level of the fuel.
Solution
New Eagle provided the engine control module, HMI display, and the engine control algorithm and software for a natural gas engine for stationary power generation.
Hardware
New Eagle selected the ECM-0563-48-0701 calibratable electronic control module for the ECM. The ECM interfaced with the components of the system and provided an interface to the HMI for field calibration of the engines. New Eagle also helped to define the components of the system and provided the systems integration expertise. By using the off-the-shelf validated engine controllers, New Eagle was able to save significant time and money as compared to a custom-built solution. By sharing common hardware and software with other systems, overall system reliability was improved.
A KAntrak 2610 module was selected as the initial HMI display unit for the system. Later, it was replaced by the VeeCAN 320 color display.
Toolchain
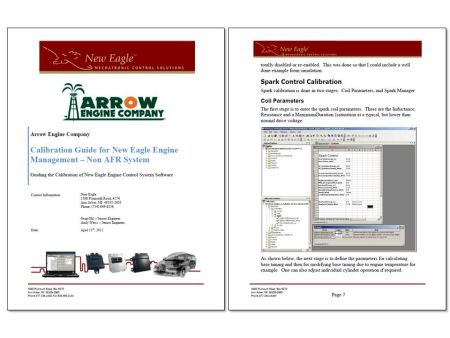
The MotoHawk and New Eagle toolchains were employed to accelerate development. Using the MATLAB/Simulink environment, the team was able to unit test and integrate the model in the simulation environment. The algorithm was then quickly deployed to the ECM through the integrated build environment.
Arrow used the MotoTune calibration tool to calibrate the engine parameters. New Eagle supplied Arrow with a calibration manual so that they could properly tune the engine for their application.
Control Algorithm
New Eagle used their extensive engine control experience and engine control libraries to develop the Arrow engine application. The development of the human machine interface was expedited through code reuse. The reuse of validated software libraries along with the base MotoHawk software increased system reliability while shortening the development cycle.
Using the same CAN interface as the calibration tool, New Eagle was able to provide calibration support through the HMI that is sold with each engine system. This allowed tuning of the engine in the field to compensate for the variability in the fuel quality. By adjusting the engine tuning, the power generator was able to operate at a higher performance level than in previous versions of the system.
Results
The natural gas engine controls were rapidly implemented and the system is now in production. New Eagle provides Arrow with fully programmed engine control modules and displays. New Eagle and Arrow are investigating improvements to the system including an auto start/stop feature.