Hybrid Truck System: Difference between revisions
No edit summary |
No edit summary |
||
Line 32: | Line 32: | ||
==Results== | ==Results== | ||
*Provides electric vehicle (EV) operation while in port for up to | *Provides electric vehicle (EV) operation while in port for up to 2-3 hours and at speeds up to 20mph. | ||
*Electric supply for auxiliary systems for up to 10 hours. | |||
*Runs in hybrid electric vehicle mode through the PTO during normal operation. | *Runs in hybrid electric vehicle mode through the PTO during normal operation. | ||
*Improves fuel economy by up to 25%. | *Improves fuel economy by up to 25%. | ||
Line 40: | Line 41: | ||
*1-1½ year return on investment in fuel savings. | *1-1½ year return on investment in fuel savings. | ||
[http://www.zeroemissionsystems.com/Video Video of the System in Operation] | |||
==Customer== | ==Customer== | ||
[http://www.zeroemissionsystems.com/ Zero Emission Systems] | [http://www.zeroemissionsystems.com/ Zero Emission Systems] |
Revision as of 16:11, 10 July 2012
__NOTITLE__
Opportunity
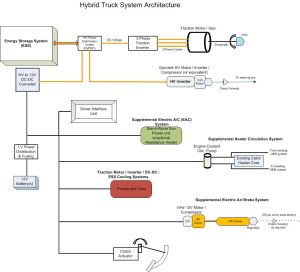
Work with Zero Emission Systems to:
- Provide the electronic controls, control algorithm and system integration for an aftermarket electric vehicle / Hybrid electric vehicle (EV/HEV) system for a class 8 vehicle (greater than 33,000 pounds).
- System operates in electric vehicle mode when in port to provide zero emissions while queuing and operates in hybrid electric vehicle mode during normal operation to provide better fuel economy.
- Integrate the system on a vehicle to provide prototype demonstration of the benefits.
- Support vehicle performance testing.
Solution
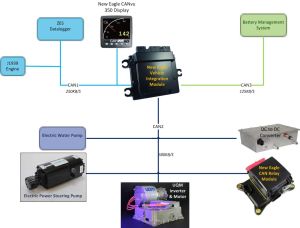
New Eagle provided the vehicle integration module, the controller area network (CAN) relay box and the vehicle integration module algorithm and software for an aftermarket EV/HEV system. We also provided extensive onsite vehicle support and system integration and verification.
Hardware
New Eagle selected the ECM-5554-112-0904 calibratable electronic control module for the vehicle integration module (VIM) and the Multiplexed Power Distribution Module (MPDM) for the CAN relay controller. The VIM interfaces with all of the components in the system through three independent CAN channels. In addition, the VIM reads sensors such as pressure and steering position, and controls outputs such as the electric power steering input control and the various system relays.
A CANvu 350 module was selected as the prototype display unit for the system. For future upgrades this display will be replaced by the more powerful and more cost effective VeeCAN 320 display.
Toolchain
Control Algorithm
Results
- Provides electric vehicle (EV) operation while in port for up to 2-3 hours and at speeds up to 20mph.
- Electric supply for auxiliary systems for up to 10 hours.
- Runs in hybrid electric vehicle mode through the PTO during normal operation.
- Improves fuel economy by up to 25%.
- Charges through the engine and regenerative braking.
- Provides high voltage operation from 403 volts to 550 volts.
- Implements a J1939 compatible CAN 2.0 link.
- 1-1½ year return on investment in fuel savings.
Video of the System in Operation