Natural Gas Engine with Variable Energy Adjustment: Difference between revisions
No edit summary |
No edit summary |
||
Line 12: | Line 12: | ||
===Hardware=== | ===Hardware=== | ||
New Eagle selected the [] calibratable electronic control module for the engine control module (ECM). The ECM interfaced with all of the components in the system and adjusted the fuel and air mixture automatically. | New Eagle selected the [http://www.neweagle.net/support/wiki/index.php?title=Controllers#48_Pin_563_Engine_Control_Module ECM-0536-48-0701] calibratable electronic control module for the engine control module (ECM). The ECM interfaced with all of the components in the system and adjusted the fuel and air mixture automatically. | ||
A [http://www.neweagle.net/support/wiki/index.php?title=CANvu#CANvu_350 CANvu 350] module was selected as for the HMI display unit for the system. For future upgrades this display will be replaced by the more powerful and more cost effective [http://www.neweagle.net/support/wiki/index.php?title=VeeCAN_320_Display VeeCAN 320] display. | A [http://www.neweagle.net/support/wiki/index.php?title=CANvu#CANvu_350 CANvu 350] module was selected as for the HMI display unit for the system. For future upgrades this display will be replaced by the more powerful and more cost effective [http://www.neweagle.net/support/wiki/index.php?title=VeeCAN_320_Display VeeCAN 320] display. |
Revision as of 15:05, 11 July 2012
Opportunity
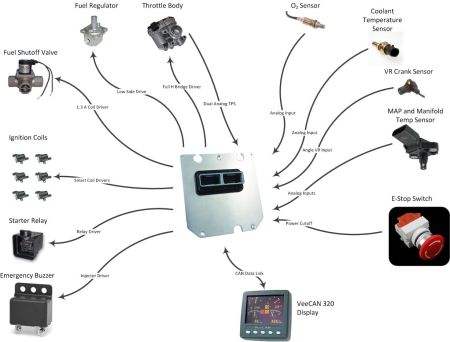
Develop the control system on a stationary natural gas engine for Arrow Engine Company. The engine provides power generation in oil and gas exploration sites and must run on the fuel obtained directly from the field. The energy content of the fuel and the level of contaminants varies from site to site. The controls were required to automatically adjust to the variation of the fuel quality.
Solution
New Eagle provided the engine control module, HMI display and the engine control algorithm and software for a natural gas engine for stationary power generation.
Hardware
New Eagle selected the ECM-0536-48-0701 calibratable electronic control module for the engine control module (ECM). The ECM interfaced with all of the components in the system and adjusted the fuel and air mixture automatically.
A CANvu 350 module was selected as for the HMI display unit for the system. For future upgrades this display will be replaced by the more powerful and more cost effective VeeCAN 320 display.
Toolchain
The MotoHawk and New Eagle toolchain was employed to acclerate development. Using the Matlab / Simulink environment, the team was able to unit test and integrate the model in the simulation environment in parallel to the mechanical hardware development. The early start on algorithm development saved several weeks off of the timeline. New Eagle also utilized the Network Toolbox to quickly implement the CAN messaging strategy.Many of the actuators and sensors had defined DBC files for the CAN control commands and output feedback. By using the Network Toolbox, the messaging strategy was quickly implemented allowing more time for the critical algorithm development.