Alternative Fuel Vehicles: Difference between revisions
No edit summary |
No edit summary |
||
Line 13: | Line 13: | ||
== Certified Heavy Duty Spark Ignited Engine == | == Certified Heavy Duty Spark Ignited Engine == | ||
[[File:LPG_engine_control.png| | [[File:LPG_engine_control.png|600px | right]] | ||
An 8.0L, V8, naturally aspirated engine from Powertrain Integration was developed to run on dedicated propane autogas fuel and installed in various Freightliner truck and bus platforms. The control system developed by New Eagle includes model-based torque estimation, torque limiters and arbitration as well as various OBD specific physical based models. The controls system is designed to be safety critical and provides redundant monitoring of critical paths. This control system has been fully certified by CARB and U.S. EPA to meet 2013 Alternative Fuel Vehicle emissions standards. | An 8.0L, V8, naturally aspirated engine from Powertrain Integration was developed to run on dedicated propane autogas fuel and installed in various Freightliner truck and bus platforms. The control system developed by New Eagle includes model-based torque estimation, torque limiters and arbitration as well as various OBD specific physical based models. The controls system is designed to be safety critical and provides redundant monitoring of critical paths. This control system has been fully certified by CARB and U.S. EPA to meet 2013 Alternative Fuel Vehicle emissions standards. |
Revision as of 18:33, 13 December 2013
Introduction
New Eagle has experience in engine controls development for a range of alternative fuels applications. There is a push towards the use of alternative fuels in the transportation industry. Fuel cost, decreased environmental impact, and domestic availability are all benefits that can be realized by using alternative fuels. For consumption of alternative fuels to increase, infrastructure and vehicle solutions must be put in place. New Eagle distributes controllers, auxiliary displays, throttle bodies, injectors and other engine and vehicle components to companies producing alternative fuel solutions. New Eagle also has engineered engine systems that respond to the demand for alternative fuel consumption. These solutions range from dedicated engine control systems to aftermarket systems.
Alternative Fuel Components
New Eagle has an extensive supplier network to provide the best validated components at competitive prices. This offering includes a full set of components required for the design and assembly alternative fuel vehicle systems.
For information on industrial parts/components please click here. or search the wiki products by application or products by category section.
Alternative Fuel Systems
There is a range of applications which allow vehicles to consume alternative fuels: dedicated systems are designed to consume an alternative fuel, engine retrofit applications convert an engine intended to use one fuel into an engine capable of consuming an alternative fuel, bi-fuel systems are designed to allow an engine to switch between primary and alternative fuel consumption in operation, mixed fuel (dual fuel) systems allow for consumption of a blend of the primary and alternative fuel. New Eagle has experience with the development of all of these types of systems for alternative fuel vehicles. The New Eagle engineering team has experience with safety-critical system development, vehicle integration, communication protocol standards, and diagnostics and this expertise is integrated into our solutions.
Certified Heavy Duty Spark Ignited Engine
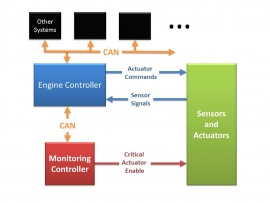
An 8.0L, V8, naturally aspirated engine from Powertrain Integration was developed to run on dedicated propane autogas fuel and installed in various Freightliner truck and bus platforms. The control system developed by New Eagle includes model-based torque estimation, torque limiters and arbitration as well as various OBD specific physical based models. The controls system is designed to be safety critical and provides redundant monitoring of critical paths. This control system has been fully certified by CARB and U.S. EPA to meet 2013 Alternative Fuel Vehicle emissions standards.
The developed Engine Control Software has the following features:
- Pedal interpretation as torque requester
- Cruise Control
- PTO Control
- Torque limiting functions
- Torque arbitration (between pedal, cruise, PTO)
- open loop fuel control
- close loop fuel control
- Airflow characterizations and dynamics
- Idle Control
- Deceleration Fuel Cutoff and safety fuel cut
- Ignition angle and energy characterization
- Engine torque characterization
- Forward path: friction and pumping losses, indicated engine torque to air charge characterization, modifiers for ignition retarding, temperature and pressure modifiers, equivalence ratio modifier, ignition angle offset request based on fast path torque, torque reserve request
- Reverse path: frictional and pumping losses, air charge to torque characterization, modifiers for ignition retarding, equivalence ratio modifier, temperature and pressure modifiers, fuel cutoff
- Slow path: throttle based slow path torque delivers nominal torque plus torque reserve request
- Fast path: spark based fast path torque delivers transient torque requests from torque reserve
- Modeled air charge
- Engine state determination
- Steady state determination
- Modeled temperatures
- Lambda
- Accessory control
- Throttle Position control
- HEGO heater control
- Injector characterization
- Ignition angle and energy characterization
- Sensor rationalities for redundancy
- Secondary microprocessor rationalities
- OBD II Diagnostics
- OBD II Major Monitors
- Fuel system monitor
- Catalyst monitor
- Catalyst temperature model
- Engine coolant temperature monitor
Bi-Fuel Gasoline Engines
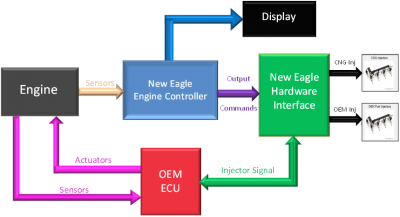
New Eagle has verified a Bi-Fuel system design which utilizes a proven off-the-shelf embedded controller and custom electronics for use in the aftermarket. The system design involves rerouting the OEM injector signals through the New Eagle system so that they can be disabled in order to allow operation on the secondary fuel. A secondary fuel system is installed with an additional set of fuel injectors which the New Eagle controller will drive.
The introduction of an aftermarket component into an OEM control loop such as fueling will inevitably introduce gain and lag. The New Eagle system is designed to minimize the gain and lag introduced to the system by allowing on-cycle fueling adjustments and calibration of start of injection of the secondary fuel. The gain and lag that are introduced can cause instability in the OEM fueling control. The Bi-Fuel controller must allow the OEM control loop to drive to the correct engine output oxygen content. This means that a properly tuned system will have a different 'pedal to power' relationship on the secondary fuel when compared to the primary fuel. The system can be calibrated to operate on one fuel or the other at different engine conditions, allowing customization of the drive areas where most displacement is desired. Future system developments aim to utilize existing OEM fuel mapping to allow for bi-fuel operation without a change to the 'pedal to power' relationship.
New Eagle is continuing to advance development of Bi-Fuel technology. We are currently investigating OBD-II compliance, both port injection and direct injection variants, and multiple vehicle platforms. .
Dual Fuel Diesel Engines
The New Eagle Dual Fuel Control System uses compressed natural gas (NG) as the fuel source. A spark plug for dedicated system to ignite the NG air-fuel charge. Dual-Fuel systems use a small amount of diesel in a standard compression ignition engine to ignite the NG. Natural Gas is introduced into the intake air flow while the throttle command is intercepted from the driver so as to reduce the demand for diesel. This reduces the need to make significant hardware changes to the engine, reducing the overall kit cost for a retrofitted engine. The control system is designed so that any failure in the kit results in a return to nominal operation of the vehicle, this reduces the risk of introduction into the critical torque path.
Diesel is replaced by NG so that during highway operation diesel flow rates can be comparable to idle operation. A torque based control model is used to control the NG and diesel injection quantities to reduce changes to the effective power curve of the engine. The displacement that can be achieved is limited by multiple factors depending on the operating condition. There is a minimum diesel quantity needed for combustion at low loads. There are over-fueling and knock limits at higher engine loads. Emissions considerations will also limit displacement; the engine's after-treatment systems must be kept in operable ranges.
Contact Us
Please contact us for components inquiries or to work with our engineering team for supporting your projects.