OBD Compliant LPG Engine Conversion: Difference between revisions
Line 6: | Line 6: | ||
[[File:School_Bus.jpg| left | 100 px]] | [[File:School_Bus.jpg| left | 100 px]] | ||
New Eagle developed the control system on a liquified petroleum gas (LPG) engine for a [http://powertrainintegration.com/ Powertrain Integration] 8.0-liter 8-cylinder engine. The system uses the 8.0L engine with an LPG fuel system from | New Eagle developed the control system on a liquified petroleum gas (LPG) engine for a [http://powertrainintegration.com/ Powertrain Integration] 8.0-liter 8-cylinder engine. The system uses the 8.0L engine with an LPG fuel system from Clean Fuels USA for the traditional gasoline fuel system. New Eagle provided torque security for electronic throttle control. | ||
New Eagle also implemented purge and evaporative emission controls for the fuel delivery system. The system is required to be OBD compliant for use in vehicles between 14,000-pound to 33,000-pound gross vehicle weight. | New Eagle also implemented purge and evaporative emission controls for the fuel delivery system. The system is required to be OBD compliant for use in vehicles between 14,000-pound to 33,000-pound gross vehicle weight. |
Latest revision as of 14:10, 28 February 2023

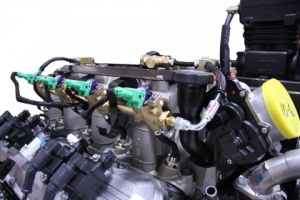
Opportunity
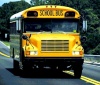
New Eagle developed the control system on a liquified petroleum gas (LPG) engine for a Powertrain Integration 8.0-liter 8-cylinder engine. The system uses the 8.0L engine with an LPG fuel system from Clean Fuels USA for the traditional gasoline fuel system. New Eagle provided torque security for electronic throttle control.
New Eagle also implemented purge and evaporative emission controls for the fuel delivery system. The system is required to be OBD compliant for use in vehicles between 14,000-pound to 33,000-pound gross vehicle weight.
The first production applications were the Freightliner Custom Chassis school bus and medium-duty delivery vehicles.
Solution
New Eagle provided the engine control module, the safety controller and the control algorithms for the engine control system. A five-phase program plan was created and tracked throughout the project. This ensured that all of the critical steps (design, DFMEA, testing) for product development were completed on time. Weekly updates were provided to the customer. New Eagle worked closely with Powertrain Integration in all phases to ensure a successful program.
Hardware
Early system development utilized the ECM-0565-128-0702 Calibratable Engine Control Module (now obsolete) for engine control algorithms. The team switched to an ECM-5554-112-0904 Calibratable Engine Control Module for later development. The calibratable module provides quick calibration through the MotoTune calibration tool. An ECM-5554-112-0904 flash module is in series production now that the calibration parameters for OBD compliance have been finalized.
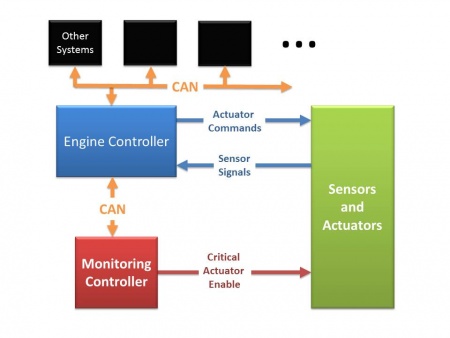
An ECM-0S12-024-0802 Calibratable Engine Control Module was implemented for the safety processor. This controller communicates with the engine controller and ensures that it is operating properly. If the safety controller detects a discrepancy, it disables critical control actuators and shuts down the system.
New Eagle is currently developing a single controller solution with an integrated safety processor. By integrating the safety processor into the engine controller, the overall cost will be decreased while increasing system reliability.
Toolchain and Control Algorithm
New Eagle used the MotoHawk Toolchain from Woodward to implement the engine controls and monitoring controls. New Eagle has an extensive library of engine control algorithms and gaseous fuel algorithms that were used as a basis for this program. By using the MotoHawk tools and the base libraries, New Eagle was able to develop the LPG engine controls quickly. Using the verified controller, base software and algorithm libraries increased the reliability and confidence of the system.
A DBC file for the engine CAN communication protocol was provided for the program. Using the New Eagle Network Toolbox Software, the team was able to quickly implement the CAN communications, saving significant development time. By ensuring that both the sending and receiving module used the same DBC file, debug time was reduced.
Results
New Eagle, Powertrain Integration and Clean Fuels USA were able to successfully convert an engine to burn LPG fuel for a production over-the-road, large, non-pivoting vehicle. OBD validation and EPA certification has been completed, and series production is scheduled for mid-2013.
- Will meet GM durability, torque and horsepower requirements
- Applications will be certified by the California Air Resources Board and the U.S. Environmental Protection Agency.
- Vehicles will comply with Federal Motor Vehicle Safety Standards and with On-Board Diagnostic requirements through 2019.