Engine and Transmission Controls: Difference between revisions
No edit summary |
|||
Line 123: | Line 123: | ||
==== Standard Engine Controller ==== | ==== Standard Engine Controller ==== | ||
New Eagle offers a pre-programmed, tunable engine controller: [[Engine_Control_System_Development_Tools#Standard_Engine_Controller|Standard Engine Controller]] | New Eagle offers a pre-programmed, tunable engine controller: [[Engine_Control_System_Development_Tools#Standard_Engine_Controller|Standard Engine Controller]] | ||
==Transmission and Driveline== | ==Transmission and Driveline== |
Revision as of 16:36, 19 April 2012
Engine Management Systems
New Eagle engineers offer system engineering and customers embedded control systems solutions including system designs, development, and integration tools and processes. Services that are provided by New Eagle include controls, production software testing, component and hardware selection and development, user interface devices, and long term customer support.
Experience
New Eagle has the following experience:
- Powertrain and vehicle modeling
- Engine calibration
- Model based controls development methods
- Engine control algorithm development including port and direct injected fuel delivery, spark advance, bypass air, torque management, electronic throttle positioning, cylinder deactivation, cam phaser positioning, and all associated diagnostics.
- Interactive transmission controls for conventional automatic transmissions, CVT, and DCTs
- Extensive experience working to OEM production requirements, and utilizing industry best practice development methods and processes.
- Experience working in partnership with Tier 1 suppliers, both domestically and internationally.
- Supplier development, evaluation, and selection
Integrated Powertrain Control
The New Eagle Engine Management Control System uses MotoHawk model-based developed tools, process, and libraries. This is carried through from prototype through production. New Eagle has utilized the basic building blocks provided in this tool to create a set of high level function libraries, which can be used to construct a complete powertrain management system to customer specifications.
Engine Control Library Blocks
The high level building blocks in the New Eagle function library are shown below, along with a brief description of the functionality contained within:
Sensors The hardware interface to all sensors, including resource assignments and basic ADC to engineering units conversions are performed here. Functions in this block include:
- analog inputs (pressures, temperatures, voltages, positions, flow rates, switch states, etc.)
- CAN inputs (same as above, but via CAN interface)
Actuators The hardware interface to all actuators, including resource assignments and basic scaling to ADC units are performed here. Functions in this block include:
- primary actuators (spark plugs, throttle body, fuel injectors, fuel pumps, "hardwired" lamps, etc.)
- secondary actuators / accessories (alternator, fan , AC compressor, etc.)
Virtual Sensors Within this block are the modeled sensors. The modeled sensors are state variables that have been created from available actual sensor information. This modeled sensor information is available to the higher level control algorithms. Examples of functionality contained within this block include:
- modeled air charge
- engine running timers
- engine state determination (cranking, running, stall, etc.)
- steady state determination
- modeled temperatures
- Lambda (wide range O2 and switch type sensors)
Diagnostics Sensors Overrides This block provides a means of replacing the sensor value with a default value when the diagnostic algorithms deem it appropriate, based on the severity of the fault that has been identified.
Base Algorithm controller This block contains the core high level functionality of the control system. It contains most of the functions required for basic engine operation. Some examples of functions contained within this block include:
- Pedal Interpretation as a torque requestor
- Cruise Control
- PTO Control
- Torque limiting functions (over-speed, over-rev, interface to transmission limiting requests, and ABS limiting requests)
- Torque arbitration
- open loop fuel control
- closed loop fuel control
- Upstream control (wide-band and switch type control available)
- Downstream control (switch type control only)
- intake airflow characterizations and dynamics
- idle control (utilizing slow and fast path torque actuators)
- Deceleration Fuel Cutoff and safety fuel cut (DFCO/FC)
- ignition angle and energy characterization as a function of speed, load, temperatures, pressures, knock, etc.
- engine torque characterization – forward path (friction and pumping losses, indicated engine torque to air charge characterization, modifiers for ignition retard from MBT as scheduled from base spark control, temperature and pressure modifiers, equivalence ratio modifier, ignition angle offset request based on fast path torque, torque reserve request and slow path / fast path coordination, DFCO/FC)
- engine torque characterization – reverse path (frictional and pumping losses, air charge to torque characterization, modifiers for ignition retard from MBT, equivalence ratio modifier, temperature and pressure modifiers, DFCO/FC).
- accessory control (fan, AC, alternator, etc.)
Component Control This block contains control algorithms linked to specific actuator hardware. functions contained within this block include:
- throttle position controller
- throttle learning algorithm
- ice breaking algorithm
- certain customer specific actuators
- HEGO heater control
Diagnostics Actuators Overrides This block provides a means of replacing the commanded value with a default value when the diagnostic algorithms deem it appropriate, based on the severity of the fault that has been identified.
Characterization This block provides conversions from engineering units to the hardware level units
- fuel mass to injector pulse width conversion (with appropriate temperature, pressure, voltage corrections)
- ignition angle and spark energy to ignition coil start and stop angles
Drive By Wire Redundant Calculations and Diagnostics This block contains all of the functionality required to validate all inputs and calculations resulting in the positioning of the throttle blade. These functions include:
- sensor rationalities with redundant and modeled sensors
- torque path calculations with redundant sensor set
- main micro checking with secondary checking micro (cross checking by each micro to monitor the state of health of the other micro)
- 3 level torque safety structure
OBD II Diagnostics OBD blockset integration aiming to be compliant with OBD II 1968.2
- Sensors: input high, input low, rate high, rate low
- Actuators: open/shorted
- CAN inputs: rate
OBD II Major Monitors and Rationalities This block contains the major monitors and rationalities. Examples of functions contained within this block include:
- fuel system monitor
- catalyst monitor
- simple misfire
- catalyst temperature model (utilized by the catalyst monitor and certain base algorithm functions).
- engine coolant temperature monitor
Communications and Reporting This block includes the interfaces required for J1939 communications, freeze frames, etc. as required for diagnostics tools and customer specific tools such as "in-plant" and "end of line". Communications interfaces to other systems are also provided, such as:
- cluster
- body controller
- transmission controller
- chassis controller
- CCP support
Standard Engine Controller
New Eagle offers a pre-programmed, tunable engine controller: Standard Engine Controller
Transmission and Driveline
New Eagle’s team of engineers has had vast experience in the development, integration and deployment of controls. With past experience - including and not limited to: Torque based Control, Chassis Powertrain Controls, Active Braking, ESP Stability, interaction based on Torque messaging, Powertrain coordination schemes optimization and more, for both diesel and gasoline engines - New Eagle, as Controls Integrators, seeks to accomplish even more challenging projects in future. We believe we have the correct solution to meet the needs of all our customers, whether it is a specific demand or a simpler challenge. Not only that, our experience over the years has given us the capabilities to ensure success with high quality of reliability, robustness, performance and support for our projects.
Emissions Controls
Ignition Driver
New Eagle offers the Woodward ignition driver, part number IGN-DRVR-001-01 / 3522-1026. Here is a pinout and description of the connectors:
-
Ignition driver pinout
-
Ignition driver connectors
The connectors are:
- Delphi Metri-Pack 150.2 female, 2 pin (CON-FEML-011A-00)
- Delphi Metri-Pack 150.2 female, 4 pin (CON-FEML-011C-01)
- Delphi connector terminals (CON-TMFL-IGNDRV-00)
Overview
New Eagle has the following experience:
- Powertrain and vehicle modeling
- Engine calibration
- Model based controls development methods
- Engine control algorithm development including port and direct injected fuel delivery, spark advance, bypass air, torque management, electronic throttle positioning, cylinder deactivation, cam phaser positioning, and all associated diagnostics.
- Interactive transmission controls for conventional automatic transmissions, CVT, and DCTs
- Extensive experience working to OEM production requirements, and utilizing industry best practice development methods and processes.
- Experience working in partnership with Tier 1 suppliers, both domestically and internationally.
- Supplier development, evaluation, and selection
Integrated Powertrain Control
The New Eagle Engine Management Control System uses MotoHawk model-based developed tools, process, and libraries. This is carried through from prototype through production. New Eagle has utilized the basic building blocks provided in this tool to create a set of high level function libraries, which can be used to construct a complete powertrain management system to customer specifications.
Engine Control Library Blocks
The high level building blocks in the New Eagle function library are shown below, along with a brief description of the functionality contained within:
Sensors The hardware interface to all sensors, including resource assignments and basic ADC to engineering units conversions are performed here. Functions in this block include:
- analog inputs (pressures, temperatures, voltages, positions, flow rates, switch states, etc.)
- CAN inputs (same as above, but via CAN interface)
Actuators The hardware interface to all actuators, including resource assignments and basic scaling to ADC units are performed here. Functions in this block include:
- primary actuators (spark plugs, throttle body, fuel injectors, fuel pumps, "hardwired" lamps, etc.)
- secondary actuators / accessories (alternator, fan , AC compressor, etc.)
Virtual Sensors Within this block are the modeled sensors. The modeled sensors are state variables that have been created from available actual sensor information. This modeled sensor information is available to the higher level control algorithms. Examples of functionality contained within this block include:
- modeled air charge
- engine running timers
- engine state determination (cranking, running, stall, etc.)
- steady state determination
- modeled temperatures
- Lambda (wide range O2 and switch type sensors)
Diagnostics Sensors Overrides This block provides a means of replacing the sensor value with a default value when the diagnostic algorithms deem it appropriate, based on the severity of the fault that has been identified.
Base Algorithm controller This block contains the core high level functionality of the control system. It contains most of the functions required for basic engine operation. Some examples of functions contained within this block include:
- Pedal Interpretation as a torque requestor
- Cruise Control
- PTO Control
- Torque limiting functions (over-speed, over-rev, interface to transmission limiting requests, and ABS limiting requests)
- Torque arbitration
- open loop fuel control
- closed loop fuel control
- Upstream control (wide-band and switch type control available)
- Downstream control (switch type control only)
- intake airflow characterizations and dynamics
- idle control (utilizing slow and fast path torque actuators)
- Deceleration Fuel Cutoff and safety fuel cut (DFCO/FC)
- ignition angle and energy characterization as a function of speed, load, temperatures, pressures, knock, etc.
- engine torque characterization – forward path (friction and pumping losses, indicated engine torque to air charge characterization, modifiers for ignition retard from MBT as scheduled from base spark control, temperature and pressure modifiers, equivalence ratio modifier, ignition angle offset request based on fast path torque, torque reserve request and slow path / fast path coordination, DFCO/FC)
- engine torque characterization – reverse path (frictional and pumping losses, air charge to torque characterization, modifiers for ignition retard from MBT, equivalence ratio modifier, temperature and pressure modifiers, DFCO/FC).
- accessory control (fan, AC, alternator, etc.)
Component Control This block contains control algorithms linked to specific actuator hardware. functions contained within this block include:
- throttle position controller
- throttle learning algorithm
- ice breaking algorithm
- certain customer specific actuators
- HEGO heater control
Diagnostics Actuators Overrides This block provides a means of replacing the commanded value with a default value when the diagnostic algorithms deem it appropriate, based on the severity of the fault that has been identified.
Characterization This block provides conversions from engineering units to the hardware level units
- fuel mass to injector pulse width conversion (with appropriate temperature, pressure, voltage corrections)
- ignition angle and spark energy to ignition coil start and stop angles
Drive By Wire Redundant Calculations and Diagnostics This block contains all of the functionality required to validate all inputs and calculations resulting in the positioning of the throttle blade. These functions include:
- sensor rationalities with redundant and modeled sensors
- torque path calculations with redundant sensor set
- main micro checking with secondary checking micro (cross checking by each micro to monitor the state of health of the other micro)
- 3 level torque safety structure
OBD II Diagnostics OBD blockset integration aiming to be compliant with OBD II 1968.2
- Sensors: input high, input low, rate high, rate low
- Actuators: open/shorted
- CAN inputs: rate
OBD II Major Monitors and Rationalities This block contains the major monitors and rationalities. Examples of functions contained within this block include:
- fuel system monitor
- catalyst monitor
- simple misfire
- catalyst temperature model (utilized by the catalyst monitor and certain base algorithm functions).
- engine coolant temperature monitor
Communications and Reporting This block includes the interfaces required for J1939 communications, freeze frames, etc. as required for diagnostics tools and customer specific tools such as "in-plant" and "end of line". Communications interfaces to other systems are also provided, such as:
- cluster
- body controller
- transmission controller
- chassis controller
- CCP support
Standard Engine Controller
Spark Ignited Engines
- Automotive quality and prices for components including sensors, throttles, and engine controllers
- Enhanced user interface for engine control and system installation and setup
- Auto Start / Stop features for scheduled duty cycle or remote engine and load control
- Fuel efficiency advantages by utilizing automotive style torque control algorithms
- OBD diagnostics to protect engine and other system components
- Adaptive to multiple fuel usage
- Adaptable controls for mobile and stationary applications
- Experience with vapor lock handling and purge routines
Compression Ignited Engines
Heavy Fueled Engines
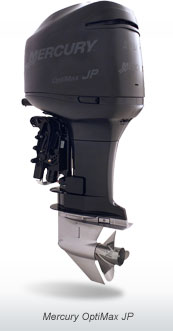
Members of New Eagle's engineering team have been working on applying the electronic fuel injection (EFI) system built in MotoHawk on UAV engines. The benefit of the MotoHawk system to the UAV is that the electronics and software have millions of hours of operation including use on the JP Marine heavy fuel engine.
One unique feature of the New Eagle EFI system is that it burns heavy fuels, JP5, JP8, and Jet A fuel. Derivatives of the EFI system have run on the UEL Rotary engine, and the xRDI Heavy Fuel engine.
The New Eagle EFI system has been developed and tested on various airframes:
- AAI Shadow
- Raytheon KillerBee
- AeroMech SandDragon
xRDI
xRDI of Beaufort, South Carolina has a number of applications using the New Eagle EFI system.
Current xRDI Projects Include:
- Engine replacement for Unmanned Aerial Vehicle (UAV), 35 hp
- Auxiliary Power Unit (APU) for business jets, 17 hp with starter generator
- Flight demonstration and engine evaluation program with major airframe supplier, 17 hp
- Flight demonstration and engine evaluation program, 35 hp
- STUAS- Tier 2, Navy and Marine joint program for ship based UAV, 15 hp
- Unmanned Ground Vehicle, 6 hp with starter generator
- SBIR Darpa Program for a 10 hp Small Engine Designed for High Efficiency, High Power Density and Quiet Operations
- Development Program for a 3-Cylinder and 4-Cylinder Heavy Fuel Engine for UAV application
Transmission Controls
New Eagle’s team of engineers has had vast experience in the development, integration and deployment of controls. With past experience - including and not limited to: Torque based Control, Chassis Powertrain Controls, Active Braking, ESP Stability, interaction based on Torque messaging, Powertrain coordination schemes optimization and more, for both diesel and gasoline engines - New Eagle, as Controls Integrators, seeks to accomplish even more challenging projects in future. We believe we have the correct solution to meet the needs of all our customers, whether it is a specific demand or a simpler challenge. Not only that, our experience over the years has given us the capabilities to ensure success with high quality of reliability, robustness, performance and support for our projects.