Alternative Fuel Vehicles
Introduction
- CARB Certified heavy duty spark ignited engines
- Dual-Fuel - Alt Fuel + Diesel Engines
- Bi-Fuel - alt fuel + gasoline Engines
Capability Overview
New Eagle has experience in engine controls development for a range of alternative fuels applications. New Eagle has developed dedicated engine control software for a heavy duty propane application that is certified by CARB. New Eagle has supported concept validation efforts for hybrid fuel systems such as mixed fuel (dual fuel) diesel and bi-fuel gasoline applications. The New Eagle engineering team has experience with safety-critical system development, vehicle integration, communication protocol standards, and diagnostics.
Example Applications
Certified Heavy Duty Spark Ignited Engine
An 8.0L, V8, naturally aspirated engine from Powertrain Integration was developed to run on dedicated propane autogas fuel and installed in various Freightliner truck and bus platforms. The control system developed by New Eagle includes model-based torque estimation, torque limiters and arbitration as well as various OBD specific physical based models. This high feature control system has been fully certified by CARB and U.S. EPA to meet 2013 Alternative Fuel Vehicle emissions standards.
Bi-Fuel Gasoline Engines
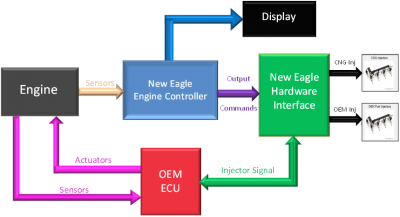
New Eagle has verified a Bi-Fuel system design which utilizes a proven off-the-shelf embedded controller and custom electronics for use in the aftermarket. The system design involves rerouting the OEM injector signals through the New Eagle system so that they can be disabled in order to allow operation on the secondary fuel. A secondary fuel system is installed with an additional set of fuel injectors which the New Eagle controller will drive.
The introduction of an aftermarket component into an OEM control loop such as fueling will inevitably introduce gain and lag. The New Eagle system is designed to minimize the gain and lag introduced to the system by allowing on-cycle fueling adjustments and calibration of start of injection of the secondary fuel. The gain and lag that are introduced can cause instability in the OEM fueling control. The Bi-Fuel controller must allow the OEM control loop to drive to the correct engine output oxygen content. This means that a properly tuned system will have a different 'pedal to power' relationship on the secondary fuel when compared to the primary fuel. The system can be calibrated to operate on one fuel or the other at different engine conditions, allowing customization of the drive areas where most displacement is desired. Future system developments aim to utilize existing OEM fuel mapping to allow for bi-fuel operation without a change to the 'pedal to power' relationship.
New Eagle is continuing to advance development of Bi-Fuel technology. We are currently investigating OBD-II compliance, both port injection and direct injection variants, and multiple vehicle platforms.
Dual Fuel Diesel Engines
The push toward the use of Natural Gas (NG) as a fuel source is being driven from multiple angles. The environments benefits of NG fueled internal combustion engines include reduced emission and the potential to use a renewable fuel source. This renewable fuel can be sourced from domestic NG fields reducing the dependency of foreign oil. The New Eagle Dual-Fuel Control System (DFCS) can also compensate for varying quality of the NG enabling the system to operate off of landfill or anaerobic pond exhaust gases. By far the biggest driver in the viability of NG as a fuel source is the economics. With diesel fuel pushing $3.80 per gallon NG fueled engines provide a significant financial benefit for long range on-highway vehicles and continuous run stationary engine applications.
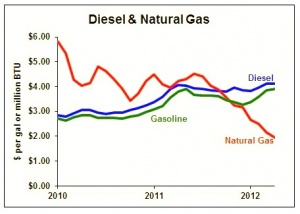
The industry has responded to the demand for NG fuel engines with a variety of solutions. These range from dedicated NG systems to Dual-Fuel system. The New Eagle DFCS uses compressed NG as the fuel source. The main benefit of this type of systems is the ease in end user integration and cost. More complicated dedicated systems require extensive hardware changes to the diesel engine to operate properly. The octane rating of NG is on the order of 120 compared to that of 15-20 for diesel fuel. This requires the integration of a spark plug for dedicated system to ignite the NG air-fuel charge. Dual-Fuel systems use a small amount of diesel in a standard compression ignition engine to ignite the NG. This reduces the need to make significant hardware changes to the engine reducing the overall kit cost for a retrofitted engine. The New Eagle DFCS is an all-encompassing solution for customers looking to convert their diesel engine to run on diesel and natural gas. New Eagle’s solution includes Human Machine Interface (HMI), data-logging, telematics and retrofit hardware. Customers can select all or some of these components to customize the kit to their needs. The interface of all the components is centered on model based system design. This allows for seamless communication and operation between the various components. This modulatory is carried over to the control strategy allowing the customer to select between varying levels of OEM integration. Some of these include cruise control, methane detection system and CAN message protocols. The New Eagle application team can put production DFCS together faster and cheaper using production intent controllers and OEM level sensors and actuators.
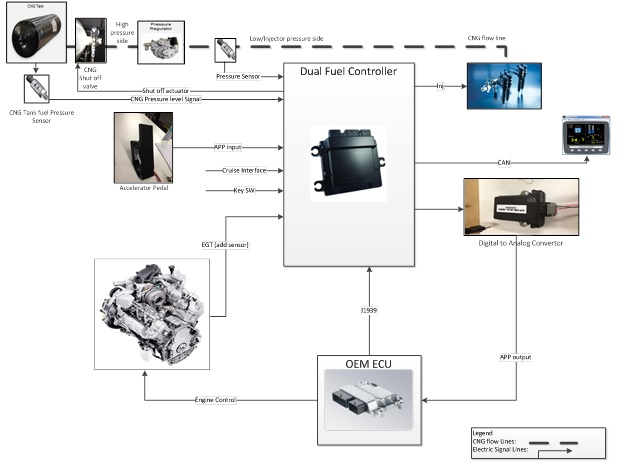
The case study of the DFCS is on a Detroit Diesel DD15 engine in a Freightliner on-highway chassis. The system utilizes a 30.2 DGE Compressed NG (CNG) tank to supply the required flow to the injection hardware. Diesel is replaced by CNG such that during highway operation diesel flow rates are comparable to idle. As mentioned previously, this small diesel charge is required to ignite the CNG. A torque based control model is used to control the CNG and diesel injection quantities to ensure that the OEM diesel torque curve is matched throughout the operating range. This is done to match the engine operating conditions for reliability and to maximize the amount of diesel displaced by the CNG. This provides the fleet operator with the greatest amount of overall fuel savings. The HMI integrated into the system is in the form of a full color LCD display. This provides feedback to the driver on the operational condition of the system, along with CNG fuel level and notifies of any system faults. The HMI is also outfitted with a data-logging system that can be set-up to to record DFCS specific variables along with any data traffic on the J1913 CAN bus at the desired sample rate. Telematics are available to download any recorded data or in a real-time mode. The New Eagle telematics solution has the added benefit of remote calibration and module re-flashing. This enables the fleet operator to remotely access the vehicle for calibration / operational updates at any time.
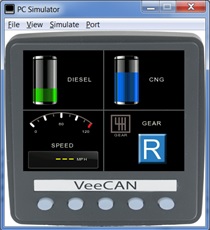
The New Eagle DFCS has potential far beyond that of the case study. The ease of installation make it a prime candidate to retrofit stationary applications as well. Without the concern of carrying large NG tanks onboard of a vehicle the DFCS can add a large amount of runtime with multiple tanks. This also can be carried over to transportation applications where space and weight are not a large factor such as locomotives and large water body shipping vessels. New Eagle can bring your Dual-Fuel retrofit application concepts to reality with our experienced team of embedded software application engineers.